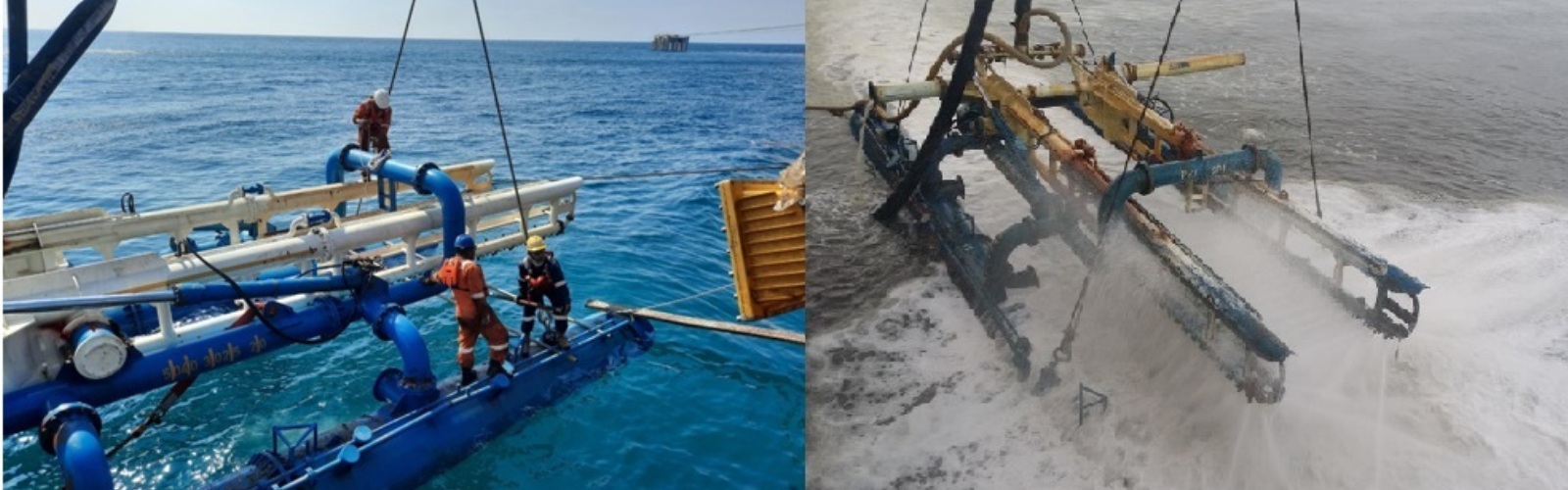
Pipeline Post Trenching
Pipeline Post trenching is a generic term for burial of the pipeline after the pipe has already been installed. It is a process where a jetting head is placed over the pipe and highly pressurised water pushed through jet nozzles to breaks up the material underneath the pipe. This material is lifted from the trench created by water eduction, airlifting or submersible pumping to create a clean trench into which the pipeline can fall.
The main elements of any pipeline Post trenching system are summarised as follows.
1. Pipeline Burial Sleds.
OCS operates the following sled arrangements.
1. Articulated Pontoon Sled
This sled is the most commonly used of OCS Jet sleds. Conceived, designed and fabricated by OCS it is deployed by crane or A frame and is self supporting on the seabed and uses articulated jetting arms with nozzle arrays to capture the pipe and direct the high pressure water at the material under the pipe. Hydraulic rams set the elevation of the arms and a further set of ancillary hydraulic arms can be directed at the soil plug directly under the pipe to prevent “wagon tracks”. Eductor / Airlift arms lift the spoil from the trench and side cast it on each side.
This sled can be used from any vessel with a crane or A frame and sufficient space to accommodate OCS equipment. The sled floats and can be pulled in to shallow areas to perform trenching in water depths the mother vessel cannot reach.
2. Trailing Arm
This is a rigid arm designed for deployment from OCS Utility Barge UB-01 “Miss Pennie”. The arm provides a rigid frame to deploy the cutting head and working in water depths to a maximum of 25 metres directs pressurised water air and hydraulics to the cutting head without the need for a hose umbilical. The system can be deployed diverlessly using scanners and does not require extensive hose umbilicals using Steel Chiksans to handle the degrees of freedom required to lower the arm and articulate the cutting head.
3. Pipe Riding Sleds
The sleds ride on the pipeline with vertically extended jetting arms and educator/ Air lifts. They are lighter and require less deck space than the articulated pontoon sled. These sleds are deployed on a job specific basis
2. Deployment A frames
For 3rd Party vessels OCS provides deployment A frames that can be dedicated to the jet sled. This frees up the vessel crane for anchor running and other activities. (The trailing arm system does not require an A frame)
3. Hose Spooler and Hoses.
For OCS Articulated Pontoon and Pipe riding jet sleds robust high pressure hose and a reliable hose deployment system are essential. OCS provides rugged hose and a deployment spooler with water Chicksan to facilitate the easy deployment and control of water, air and hydraulic hoses.
4. Water Distribution Manifold
A dedicated water distribution manifold is provided to direct feed water to the pressure pumps and return pressurised water to the hose spooler / jet sled or trailing arm with an overboarding facility for pump testing. This manifold is configured with all the necessary valves
5. High Pressure Pumps
The key to effective pipeline post trenching is the supply of high volumes of properly directed pressurised water. OCS has invested heavily in large pumping skids for this purpose. As noted above all pumps are contained in heavy duty structural skids. OCS has a total of seven (7) high volume / high pressure pumps skids in inventory. Four units are equipped with high spec solid stainless steel 5 stage centrifugal fluid ends while 3 are 4 stage centrifugal units with a lower pressure rating. The 5 stage pumps have a multiplier gear box between the power train and the fluid end to increase pump shaft revolutions.
Pressure pump skids are selected by OCS depending on the parameters of specific project such as pipe diameter, burial length and depth and geotechnical conditions. Where hard material is anticipated 5 stage pumps provide an excellent solution where as for softer material the 4 stage pumps remain a very efficient option.
OCS will evaluate and make pump selection in a project on a case by case basis.
6. Feed Pumps
Pressure pumps operate best when feed water is delivered to them at a positive pressure.
OCS provides options for electrically driven submersible pumps or diesel driven centrifugal pumps delivering water volumes to the capacity of the pressure pumps at approximately 30 psi
7. Air Lift Compressors.
High volume compressors are required for efficient airlifting. OCS would normally provide 2 x 1070 x 350 cfm compressors from in-house inventory although 3rd party units can be provided where necessary.
8. Power Generation.
3 phase power is required to power submersible pumps. OCS can utilise power from the mother barge or provide an in-house 150 kVa generators.
9. Deployment Barge for Post Trenching Equipment.
OCS UB01 Miss Pennie has been constructed specifically for nearshore projects and to accommodate OCS Pre and Post trenching equipment. However the equipment is often deployed on 3rd party barges. A robust mooring system with centralised control is required ensure the vessel can track along the pipeline at an average speed of 1.0 metre/minute. In addition cranage to handle OCS equipment packages, crew accommodation, power generation system are need to be considered during planning and preparation for post trenching projects.
PIPE BURIAL EXPERIENCE
OCS has undertaken numerous major post-trenching projects for different customers;
- JAWA-1,Combined Cycle Gas Turbine Power Plant (1760MW) Project for consortium PT Pertamina, Marubeni and Sojitz, via PT Meindo Elang Indah. Burial of 10.6km of 20” pipeline to a 2m Top Of Pipe, using OCS pontoon articulated arm jet sled deployed from the work barge Kalinda which is equipped with 8-point mooring system (2021)
- Jankrik for ENI. Burial of 42 km of 24” / 4” Piggy back to varying TOP from 0.5 metres to 2.0 metres using a pontoon articulated arm jet sled. Work from two moored vessels and DP vessel for two contractors (2016 / 2017).
- Husky BD for HCML (Indonesia), post trench of 16″ x 1.0 km, 2.0 metre TOP (2016)
- Thai Binh for PVGAS, Vietnam, post trench of 10km length of 12” pipeline for the gas distribution project. Main contractor is Sapura Kencana.(2014)
- Ketapang Petronas offshore Gresik in Surabaya, post trench of 27km of 12” pipeline to 2m TOP (2013)
- Pertamina EP MOL 12” Pipeline near Cirebon in Central Java Indonesial. (2013)
- CSJV/Chevron Australia (DOMGAS 20″ pipeline project) 2012, 20″ CWC pipeline x 25km burial distance (in combination with intermittent rock bolting), 0.5/1.0m TOP cover. Karratha, Western Australia, Australia (2012)
- HESS Indonesia (Ujung Pangkah Phase 1) 2010, 6″ CWC, 12″ CWC & 16″ CWC pipelines x 5.5 km burial distance each line, 2.0m TOP cover.Nearshore north of Gresik/Surabaya, East Java, Indonesia(2009)
- APD/Salamander (Serica Kambuna Development project) 2009/10, 14″ CWC pipeline x 13 km burial distance, 2.0m TOP cover. Nearshore north of Medan, Sumatra, Indonesia (2008)
Pipeline Post Trenching Pre Qualification Document: Download
Utility Barge and MultiCat Pre-Qualification: Download